Shaping the future into fine parts
One Stop Forging Solutions

A professional forging supplier with ISO 9001:2015 certification, we have
xtensive forging expertise in hot forging,die designing, engineering expertise, cost saving designs and manufacturing capabilities, which makes us one of India’s leading forging manufacturers. We have more than 35 years of experience in manufacturing,
a wide range of high performance, critical, electrical, and safety components, focusing on Brass, Copper, Aluminum, Mild Steel, etc providing a full range of
services, from concept to product design, engineering, manufacturing, testing, and
verification.
Aluminum Forging

Brass Forging
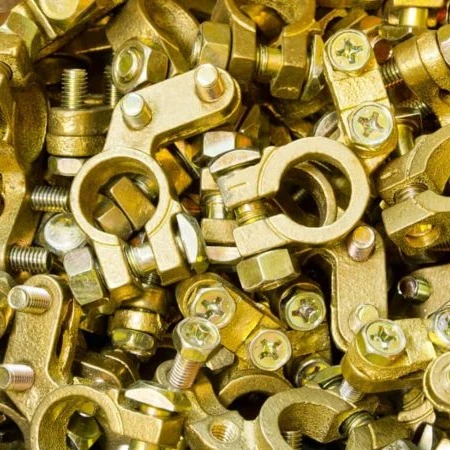
Copper Forging
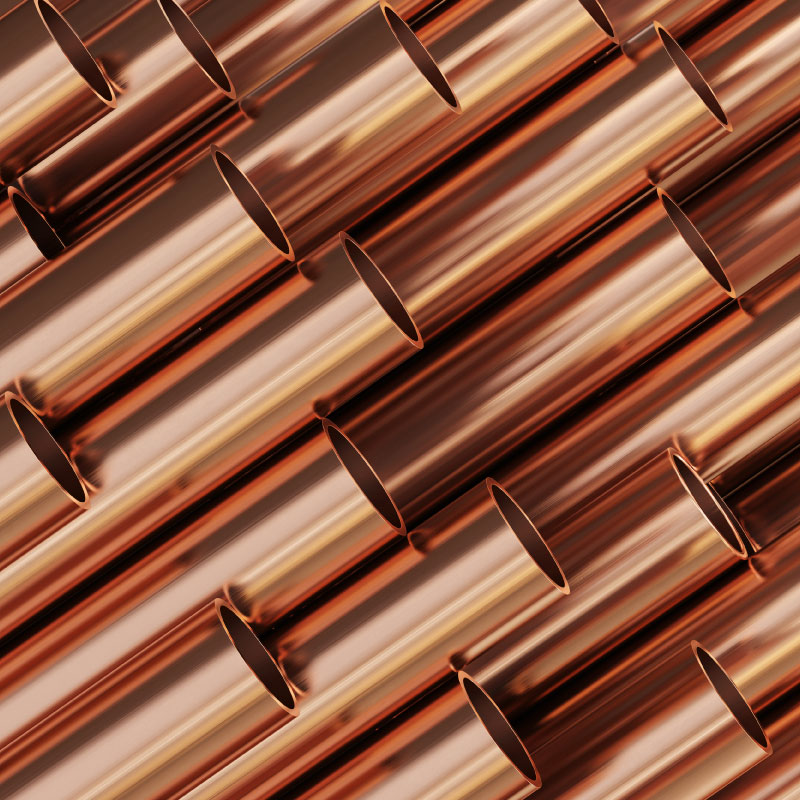
MS Forging

High Strength
High Strength
In making a forging, the metal is worked twice under tremendous pressures-first during rod extrusion and then
during forging. The double working under pressure compacts the metal and produces a very dense and refined
grain or fiber structure.
The tensile strength of the parts is thereby increased, and resistance to impact and abrasion is enhanced.
Close Tolerances
A forging produced in a steel die with close tolerances offers several advantages. Overall part dimensions are
held closer than in sand casting. Dimensions show minimum variation from part to part and permit automatic
chucking and handling in subsequent operations. The precise designs on the die surface can produce sharp
impressions on the forging surface, which is not economical with other forming processes.
Leak Resistance
The dense non-porous forged metal permits the designer to specify thinner sections without the risk of leaks
due to flaws and voids. Often the thinner forged parts result in lighter weight and lower piece cost compared to
other forming processes.
Low Overall Cost
Mass production of forged parts lends itself to maximum savings. However, smaller quantities of copper alloy
forgings can also prove economical when specific design problems must be solved. These problems include
leak integrity, close tolerances, high strength with low weight, and non-symmetrical shape.
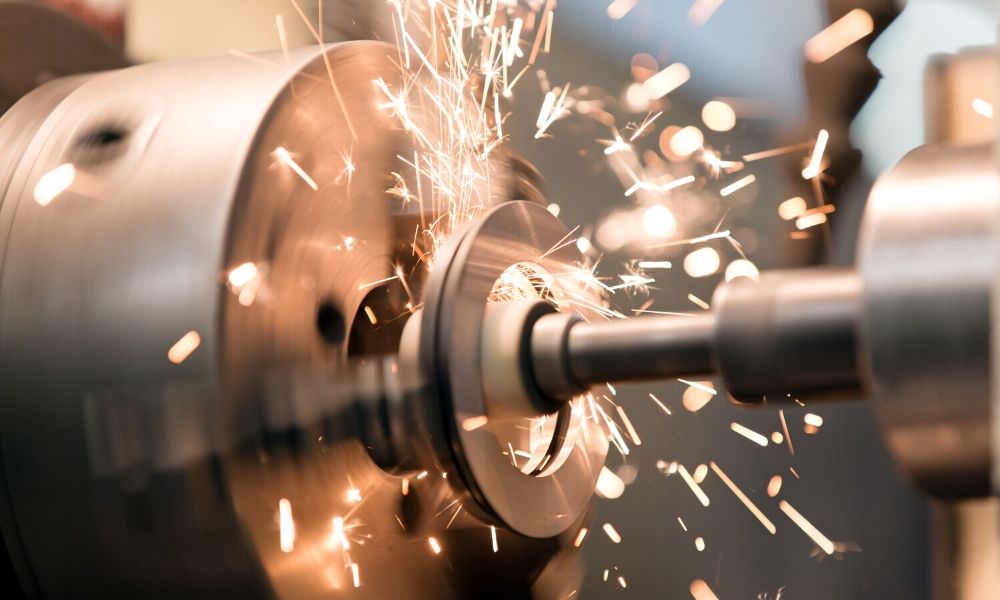
One Stop Machining Solutions
Machining, which includes drilling, tapping, milling, grinding, etc., is often combined with
forging to produce a final part so Machining is an additional process we offer to our clients to
ensure one stop solution for their product. This is a process we handle on behalf of clients
with absolute confidence regarding their products quality, requirements and dimensions.
We have the latest machineries which will ensure finest of the details and requirements are
fulfilled in minimal time.
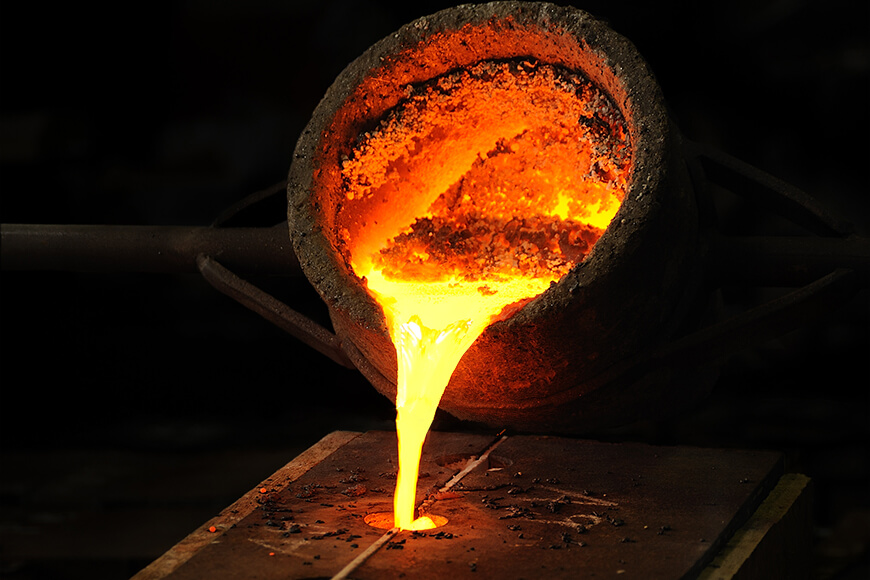
One Stop Casting Solutions
Castings provide great flexibility for the production of non-symmetrical parts.
Compared to forgings, casting surfaces tend to be rougher and tolerances tend to
be greater, and sand inclusions and porosity are sometimes encountered. Where
quantities are limited, pieces weigh over 15 pounds and casting surface
roughness and tolerances are acceptable, castings would be the economical
alternative that we can offer for our clients.
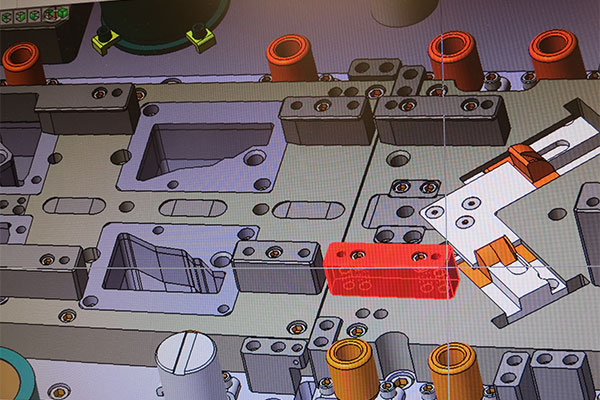
Dies And Die Designing
This is the most important and foremost step in developing a forged part, the
design engineer should be familiar with both the limitations and the flexibility
inherent in the use of a die to hot form a part.
During each forging operation the dies are subjected to high temperature metal
being forced across the die surface. Our dies are therefore made of special alloy
tool steels which can be hardened to withstand the temperature and pressure
cycling required. The average life of a single cavity die is approximately 15,000
pieces, depending on part tolerances and design. Our Engineers with their
designing expertise make sure to save the cost of the raw material of the final
product and increase the quality of the same.
Get In touch
(518) 399-4188
available from 10:00 – 19:00
Address 3212 River Rd, Frankfort, MI, 49635
Email contact@company.com